Ancillary Equipment
Every screening system needs additional equipment
A screen or screening system needs ancillary subsystems to function. Each project is determined what is needed and how far one wants to go with, for example, the automation of the system, including the removal of the waste.
Supporting and additional systems are for example:
- Spray water systems and wash water pumps
- E & I equipment (electrical control cabinets, etc.)
- Trash baskets
- Cathodic protection systems
- Conveyor systems
We would be happy to discuss your project with you! Below you can find more information.
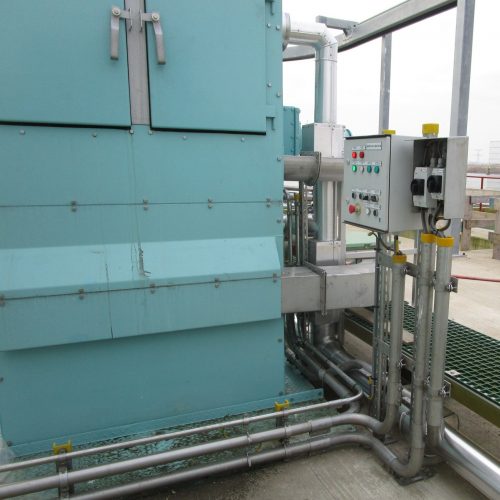
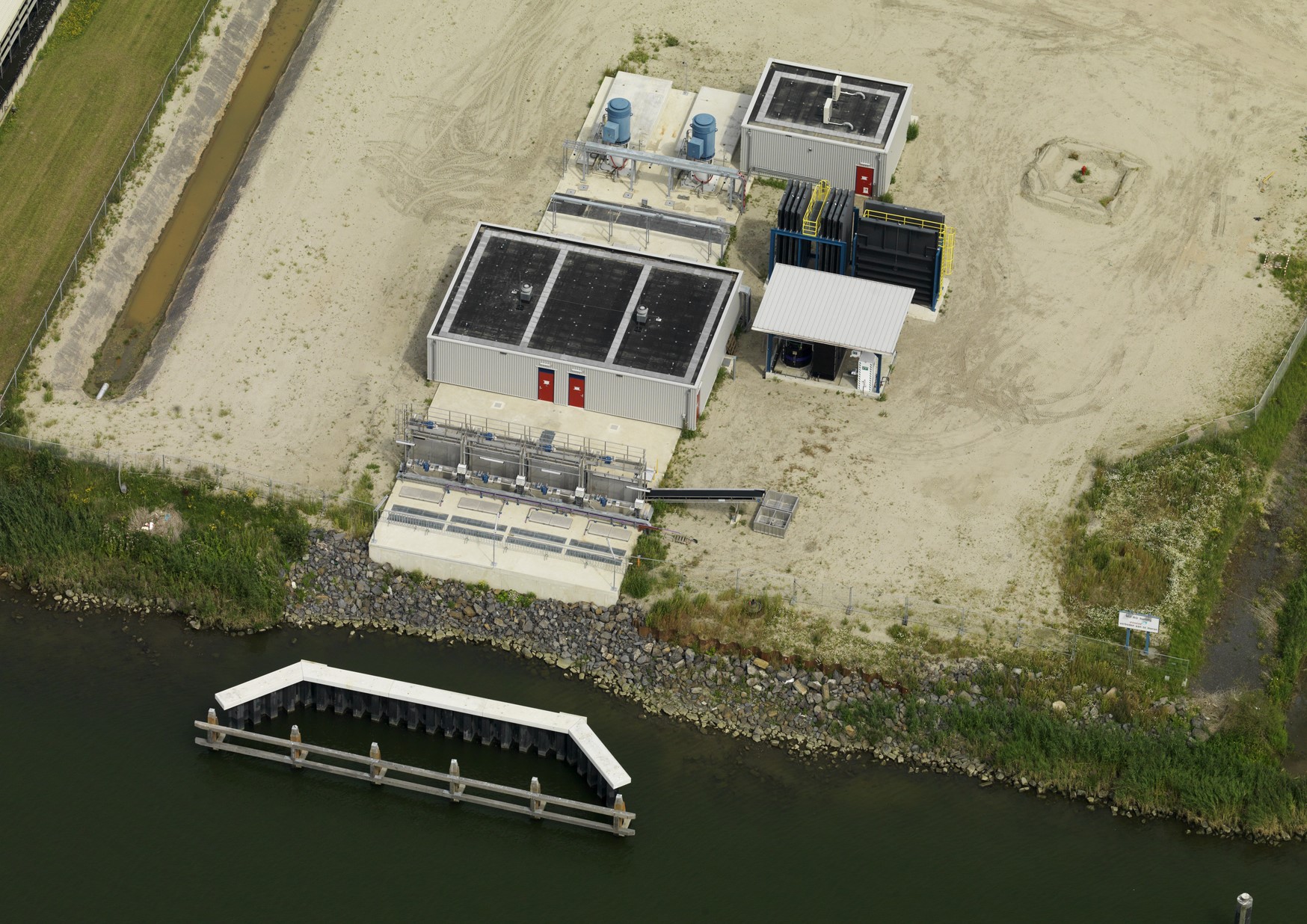
Water Intake Systems
We are specialised in water intake systems for cooling, drinking and process water
Our water intake systems are used for mechanically clean water extracted from the sea, rivers or lakes. This filtered water is applied for cooling and process water. We supply engineered, made-to-measure automated screening machinery and complete screening systems. We supply complete complete ‘screening trains‘ including all additional equipment, like controls and cathodic protection. This movie includes an animation of a typical water intake, showing the water flow from the suction from the sea to the arrival at the pumps.Â
We are active in both new construction (EPC) projects and renovation and optimization of existing water intakes.
Spray Water Systems
Compilation of nozzles, pumps, valves, controls and piping
Rotating filters, used in water intake systems require (continue) cleaning. The debris being accumulated at drums screens or travelling band screens (also called travelling water screen) is being washed off by spray water nozzles. Different configurations are possible when it comes to pumps.
In an intake system with multiple screens, each screen’s washing water system can be fed by a dedicated pump. All screens can also be fed via a central distribution system by several pumps. The screens can also be fed from an external pressure water source (this is often possible at a minimum water pressure of approximately 2.5 bar).
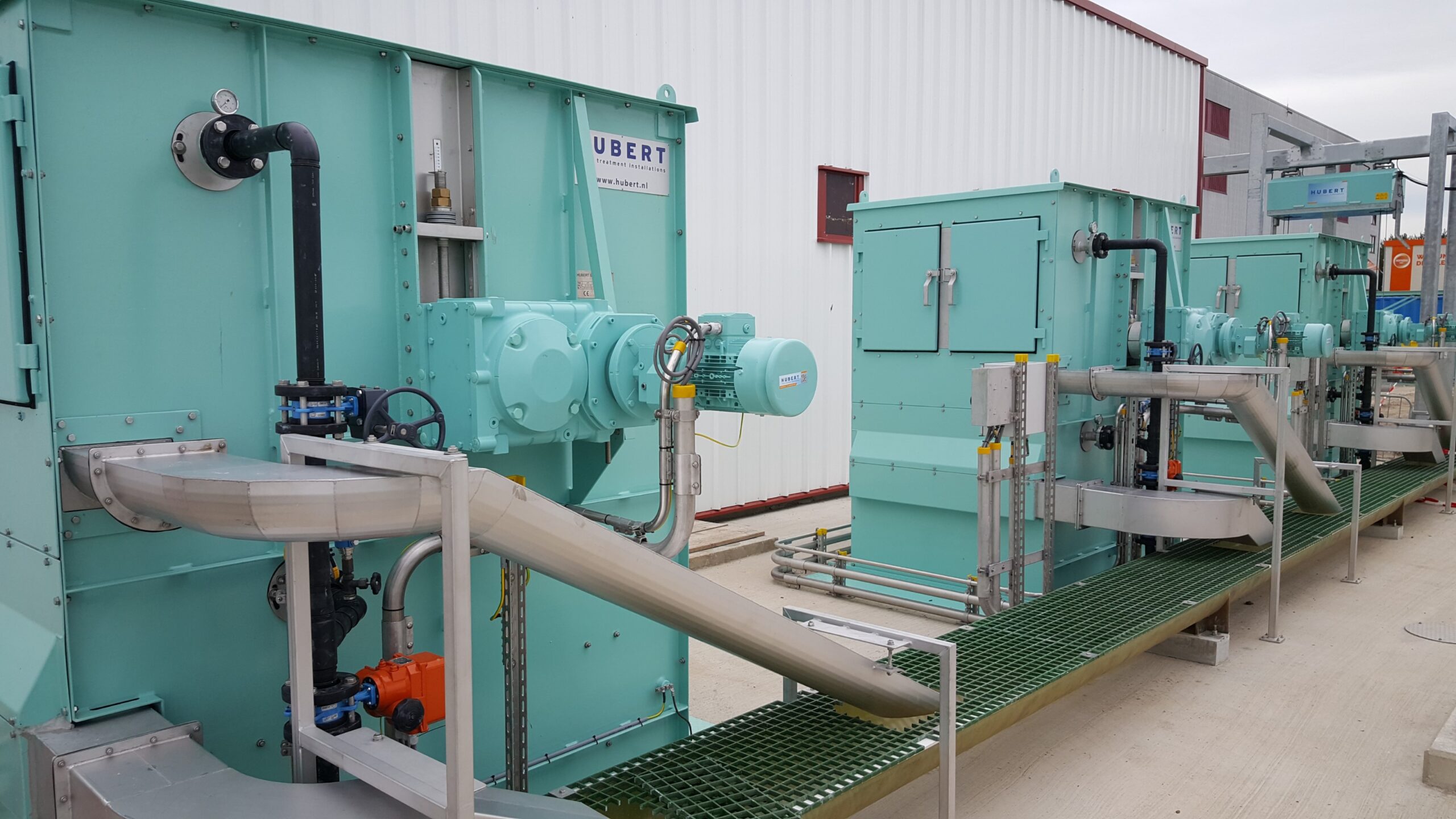
Great variety of pumps
Also with regard to the type of pumps (in combination with control valves) there are various options, depending on the project specification and the wishes of the customer. Examples of pumps used are self priming pumps, vertical shaft pumps, booster pumps and submerged pumps.
Frequently used materials for pumps include cast iron, stainless steel and exotic alloys (a variety of (super) duplex grades). Carbon steel (fresh water) or HDPE or GRP (sea water) is usually often for piping.
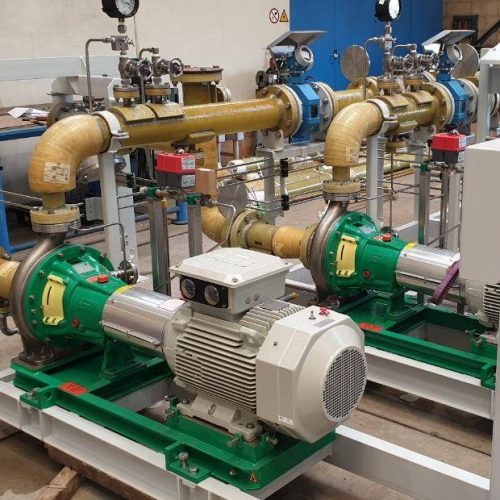
Electrical and Instrumentation (E&I)
The control is the heart of a machine
It is essential that this is properly configured and fits into the overall control system of a factory. This may involve full or partial automation. It is important to clarify before the project starts which functionality is expected.
- What is the control philosophy of the system?
- What is the degree of redundancy?
- Which standards apply?
- What kind of segregation is required?
The P&ID is a useful guide in this inventory. Hubert supplies all the necessary (Siemens) controls that are required for the machines we supply. Communication with all relevant systems is also possible.
In a screening system is cleaning also part of the control system and can be controlled in various ways, using differential level control systems.
The essence of E&I are the control and display configuration and the Motor Control Center (MCC). In addition, Local Control Panels (LCP), switches and sensors are of course part of the system.
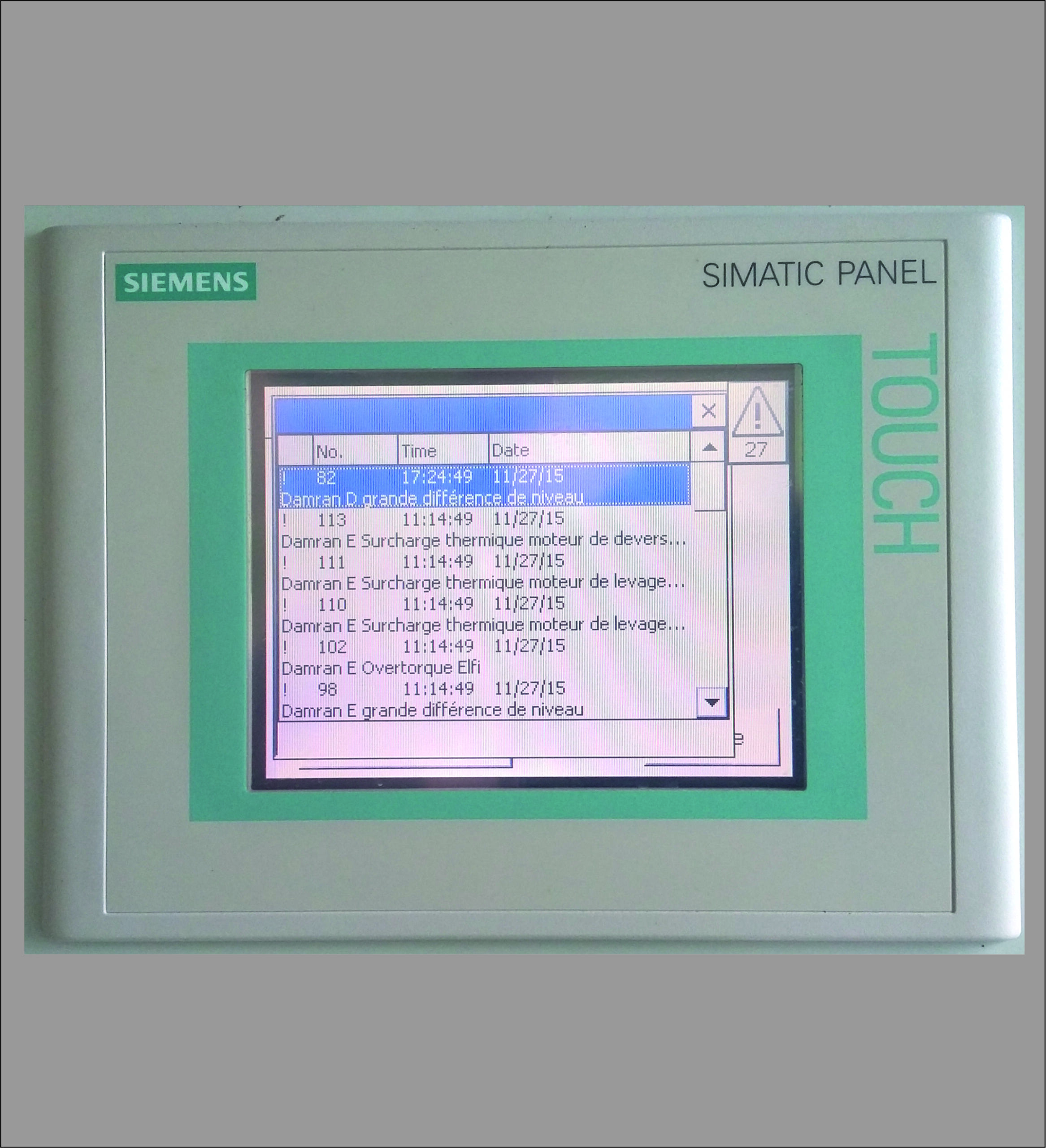
Control and display configuration
In most cases a local PLC will be sufficient. This allows the machine to be operated.
A machine can also be controlled via DCS. This usually means that no local PLC is required. Control no longer takes place locally, which can result in connection with middleware systems taking more commissioning time.
Motor Control Center (MCC)
In larger plants, an MCC is often centrally installed and several machines use it. The size and capacity therefore depends on the requirements of the customer and the local situation. Variable frequency drives for the motors are generally part of the MCC configuration.
If desired, we can supply control cabinets that include the power control in a separate compartment or the motor controle center (MCC) in a separate cabinet.
We will of course help you to come to the correct specification.
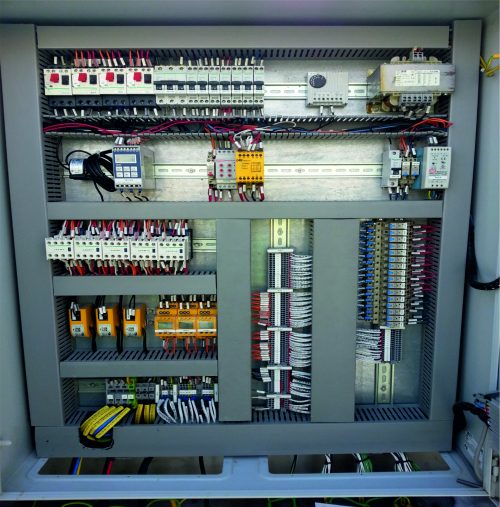
Trash Baskets
Screening systems deliver debris to be stored
Debris removed from a screening system has to be discharged. For this purpose there are various options for storing debris.
In addition to a concrete gutter or a container, we also supply a wide variety of trash baskets. Often we can draw on a standard Hubert design, but we can of course also design and manufacture a dedicated solution for you.
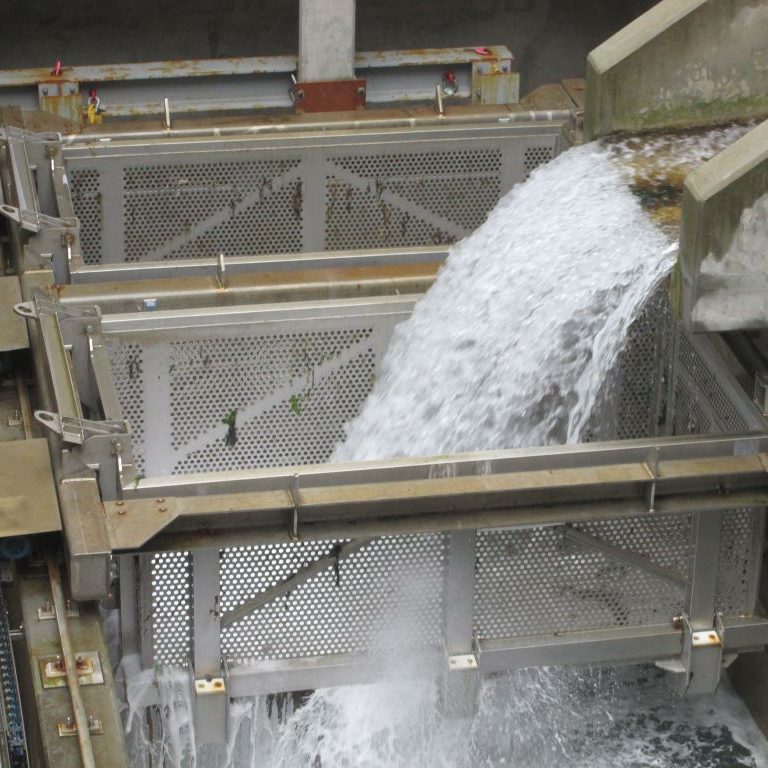
Cathodic Protection
Advanced systems for guaranteed protection
Water intake systems can be protected with sacrificial anodes or ICCP systems. Sacrificial anodes are maintenance free, but if the asset’s lifetime is to be extended beyond the anodes’ calculated lifespan, other protection solutions are required. ICCP systems not only guarantee a sufficient level of protection, but also allow for real-time monitoring of the underwater electric potential and the system’s output.
The application of sacrificial anodes is a passive protection method that doesn’t accommodate for changed circumstances such as coating damage. Their volume is also calculated for a specific lifetime, after which they need to be replaced.
Impressed Current Cathodic Protection (ICCP) systems consist of one or more reference electrodes and several ICCP anodes which are all connected to a power unit. The reference cells measure the underwater electrical protection potential and based on this data, the power unit regulates the required output to the anodes. The resulting impressed current prevents the corrosion process from taking place. A correctly installed, operated and serviced ICCP system can function & monitor real-time for 25 years or more. We can configure ICCP systems from standard components or work out a custom-built solution for your water intake project.
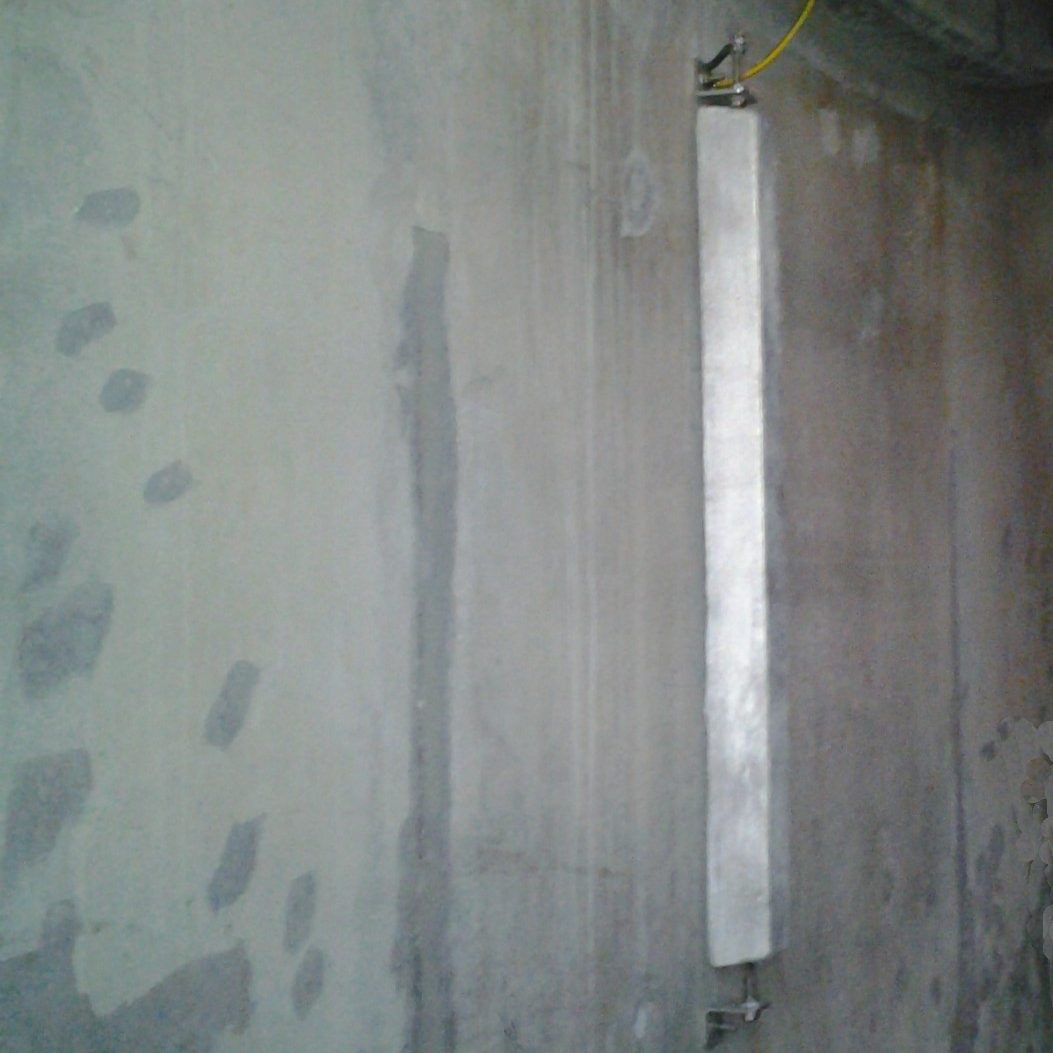
Conveyor Systems
Transport systems are often required for removal of debris
In a water intake system there are often transport systems required. In addition to gutters (embedded in the civil construction), all kinds of complementary transportation systems may also be needed. We can assist and provide the most adequate solution.
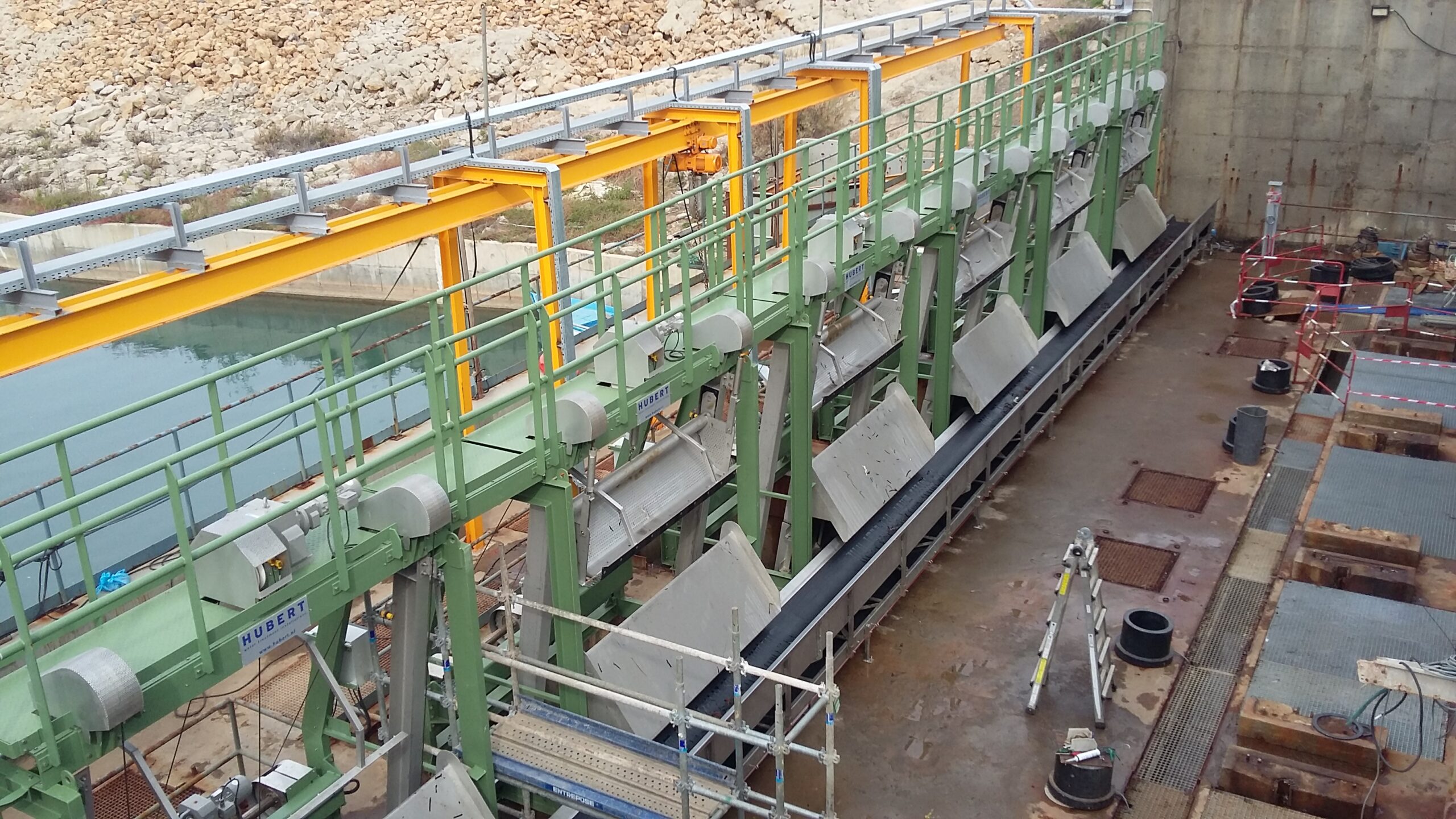