Service and After Sales
Keeping your water treatment machinery operational!
Service of water treatment machinery like water intake systems or waste water treatment thickeners, clarifier and surface aerators is our daily work. Our Service and After Sales division proves its importance by keeping Hubert installations operational anywhere in the world. We also provide service to water treatment machinery supplied by third parties.
The large amount of projects that we have carried out over the years has resulted in a huge installed base of equipment. Many of these are still in operation! We supply parts but also provide optimization and renovation of your existing equipment.
Below you will find a brief explanation of what our service organization can do for you. Visit also our pages Case Studies and Downloads.
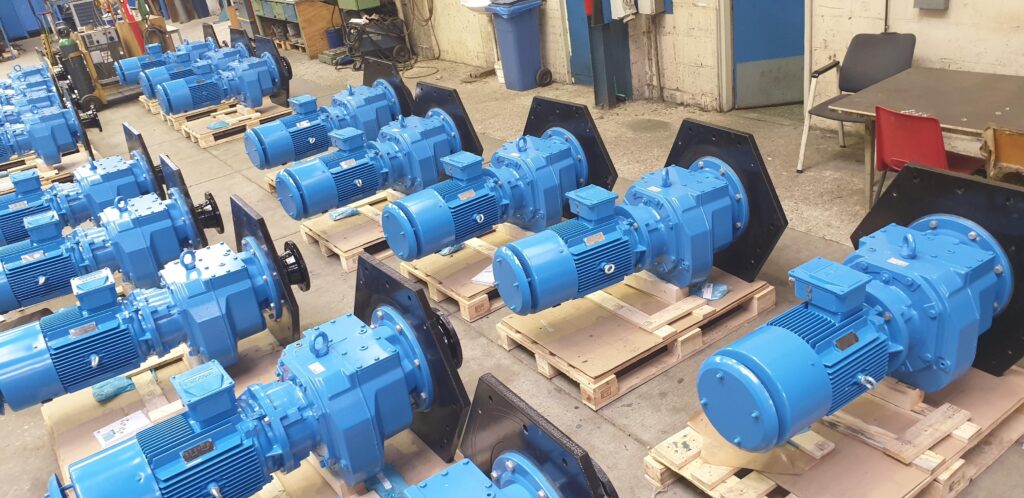
Malfunction and Repairs
Our team assists in resolving malfunctions and together with your first-line local service organization, we try to find a solution as quickly as possible. Newer generation machines may be able to diagnose remotely.
If necessary, we can have a qualified technician on site relatively quickly.
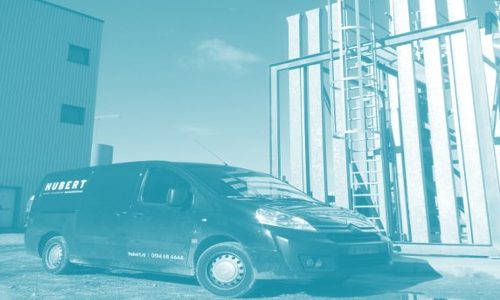
Spare and Wear Parts
We supply spare parts for equipment made after 1950!
We distribute a complete range of spare and wear parts for all machinery that have been delivered anywhere in the world. Thanks to our well maintained archives we can still manufacture and supply spare parts for equipment made after 1950, manufactured by: Hubert Sneek, Esmil Hubert, Stork, Vivendi and US Filter.
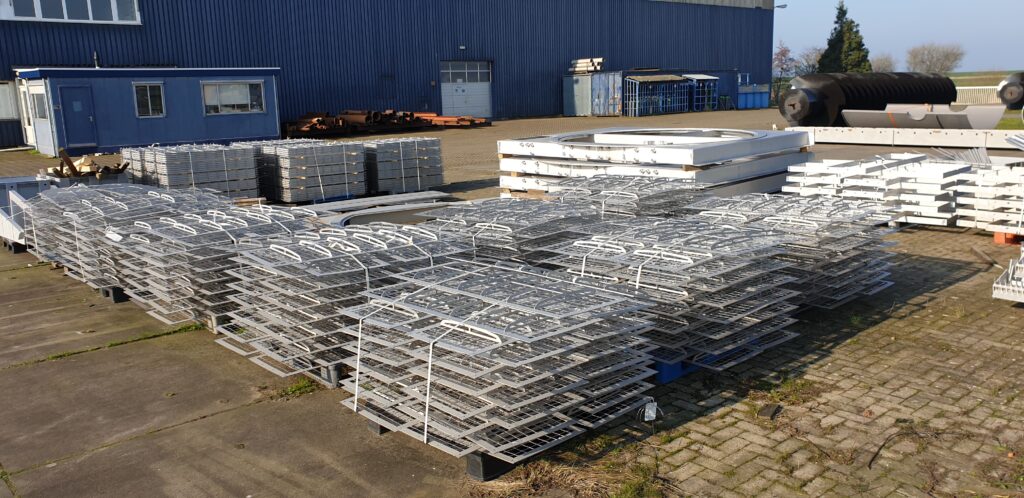
Technical Support and Training
Technical support and training on site worldwide!
If we do not take care of the installation of our equipment ourselves, our supervisors will assist your local technical team during this work.
Our service technicians and engineers provide technical support and training on site worldwide. We can train your operators to keep your machinery up and running. This requires the right knowledge! This can be a basic explanation or a made-up program especially for your type of machines. We are happy to talk to you!
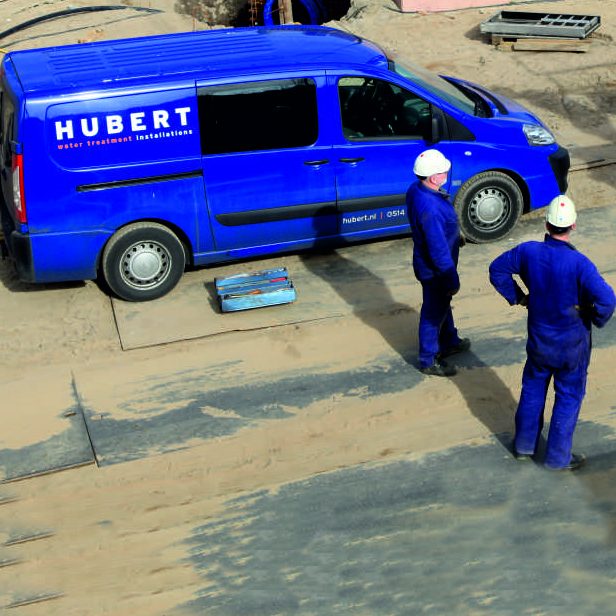
Optimisation and Retrofits
Extend service life at the lowest operating costs!
If your installation does not function optimally, this may result in an non-optimal production process. Optimistion leads to better control of your machinery and lower cost.
Optimistion of your installation can possibly be combined with a renovation, but can also be carried out separately.
A number of typical components can play a major role in renovations. These are parts that have been subject to wear and tear through years of intensive use that replacement or overhaul is necessary. You can think of rollers, frame construction, bearings, chains, pumps and gearboxes and of course the hydraulics / pneumatics and controls of an installation.
Small-scale renovation and optimisation can be carried out by our Service and After Sales division. In this case it involves renovating or updating existing components. If there are complete machines or systems including controls, we can deploy a project team.
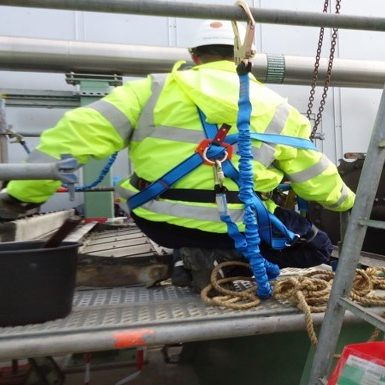
Rental of (floating) surface aerators
Hubair™ rental aerators with or without floating device
In order to fulfil the growing demand of temporary aeration installations, Hubert offers the possibility to rent floating surface aerators, with or without the floating construction. Please contact us for more information.
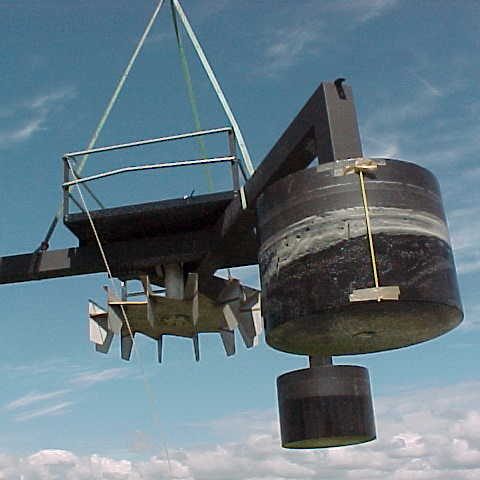
Customer Stories
Project: Replacement of gutter and clearing bridge settling tank at WWTP Birdaard
The elaboration of the drawings with accompanying calculations in the preparation phase were well worked out. The construction of the new gutter and bridge was installed satisfactorily by employees and especially the foreman. The project was completed on time, both financially and in the delivery of product certificates and revision. A great project and end result was achieved through synergy between client and contractor.
Wetterskip Fryslan, Netherlands, mr. R.T. van der Zee, Design coordinator – Director