Screening Services
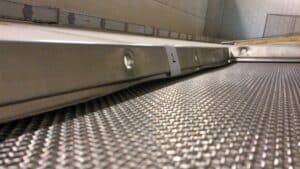
Checks and Tests
Testing screening key components
When required, we conduct thorough testing on key water screening components used in water intake systems. These tests are designed to demonstrate that the equipment meets the required performance parameters under the various load conditions it will face throughout its operational lifespan.
Below are examples of potential tests that can be conducted.
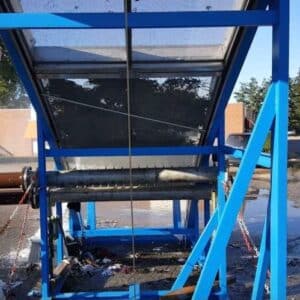
Performance Test
Simulation of spray water cleaning system in operation
The filter mesh panels of a drum screen, an integral part of a water intake system, are dimensioned based on the size of the screening installation. Key factors influencing their design include water flow and water levels. Debris captured on the panels is efficiently removed using high-pressure spray water nozzles. The removed material is then collected in a dedicated facility designed to handle and dispose of debris effectively. To ensure optimal performance, the functionality of a proposed spray water installation can be simulated and validated in real time. This testing considers factors such as the degree of contamination and the rotation speed of the drum screen.
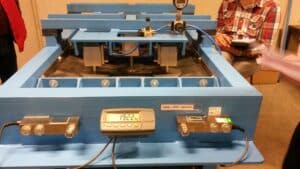
Structural Test (1)
Dynamic pressure (metal fatigue) on filter mesh
Filter mesh panels are crucial components of drum screens in water intake systems. Installed along the drum’s circumference, they filter water as it flows through, with debris removed by high-pressure spray water jets. To ensure durability, the panels undergo testing for deformation and performance under pressure cycles, simulating their expected lifetime. Displacement, pressure, and temperature are monitored during tests, which can be witnessed by clients. For example, these tests have been conducted for nuclear power plants in France, ensuring structural integrity and reliability in critical cooling systems.
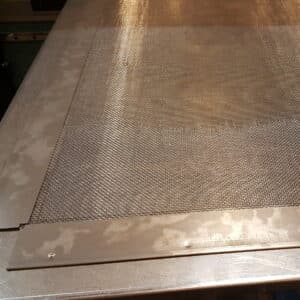
Structural Test (2)
(Static) water column on filter mesh
A water pressure test is another example of a structural evaluation. Its purpose is to validate the screen design by confirming that the theoretically calculated water pressure is accurately achieved. This is simulated by creating a water column equivalent to the permissible water pressure on a fully blocked screen segment.