Flow Patterns Drum Screen
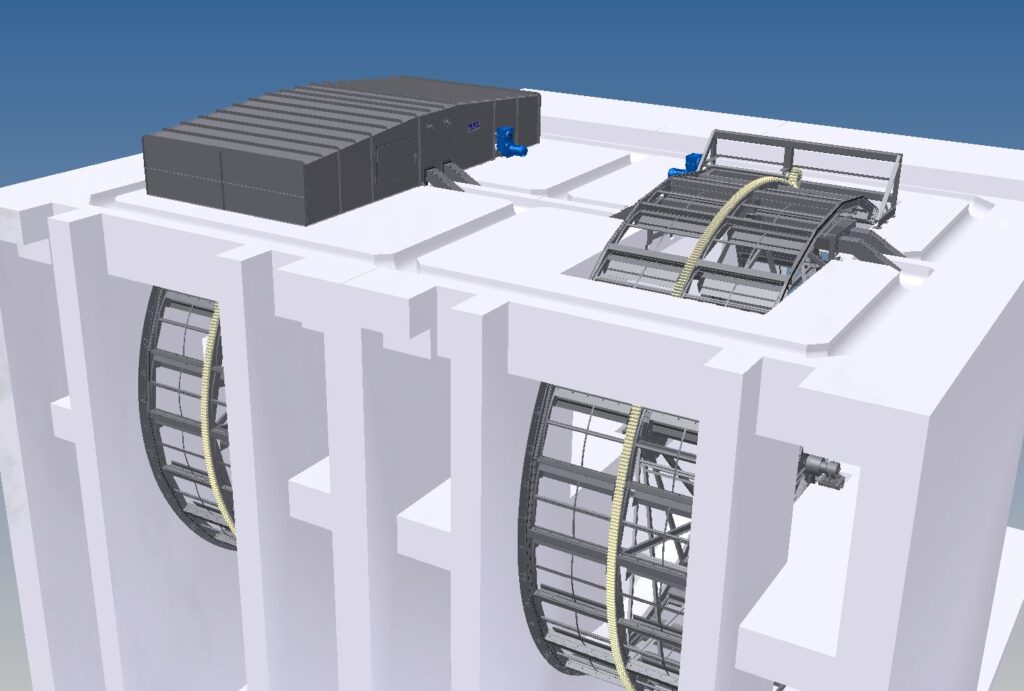
Dual Flow vs Centre Flow
Hubert designs screens based on dual flow or centre flow
A ‘Dual Flow’ configuration has some advantages over ‘Centre Flow’. In case of a newly built plant, Hubert advises the ‘Dual Flow’ pattern.
Hubert supplies both ‘Dual Flow’ and ‘Centre Flow’ pattern. Dual flow is often chosen for new plants. Centre flow is mostly used in renovation and retrofits projects. Hubert has extensive experience with both configurations.
Below you can find a comparison in drum screen flow patterns. Please contact us in case of questions.
Vertical Drumscreen – Flow Patterns
The diagram below shows the difference between dual flow (inside to outside) and centre flow (outside to inside).
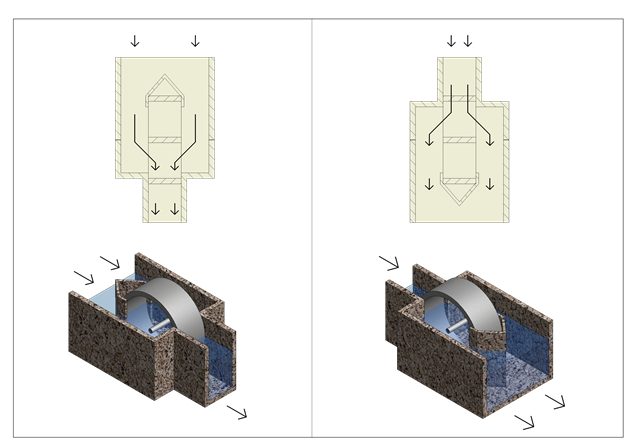
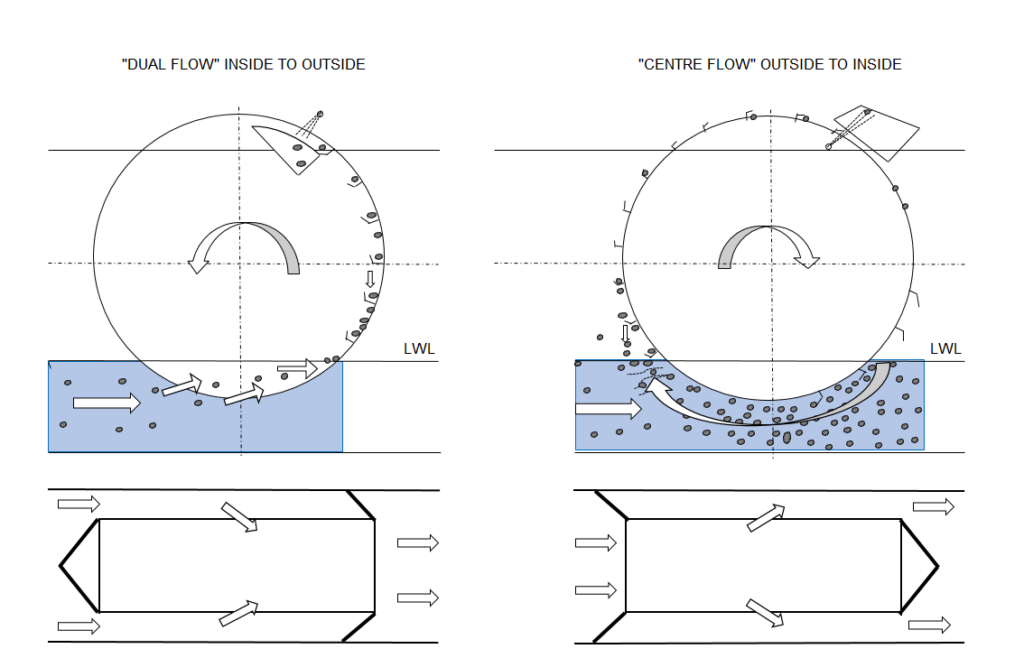
Comparison of drum screen flow patterns
Flow configuration
Dual Flow
The raw water stream enters the drum screen at the inside off the drum. And will guide the water through the mesh panels. The filtrated water leaves the drum screen central. The debris will be collected at the inside of the drum. This flow pattern will result in a laminar flow downstream.
Centre FlowÂ
The raw water stream enters the drum screen at the outside of the drum and will guide the water through the mesh panels. The filtrated water leaves the drum at both sides off the drum. The debris will be collect at the outside of the drum. This flow pattern will result in a more turbulent flow downstream.
Debris collection efficiency
Dual Flow
The debris will be collected at the inside off the drum. By the use of debris carriers the debris will slide into the debris hopper by gravity. This will result in a positive debris removal in case of dense trash, jelly fish, and fish recovery.
Centre FlowÂ
The debris will be collected at the outside off the drum. At low tide the drum screen has to be submerged for at least 1/3 diameter otherwise debris, which sticks to the mesh in the lowest part, can fall back or is flushed away by high speed rotation/ flow before the retaining lips. This can cause accumulation of debris, jellyfish and other biomaterial.
Debris and Wash water collecting hoppers (maintenance)
Dual Flow
The debris hopper can be inspected and cleaned from operation floor on both sides.
Centre FlowÂ
The debris hopper can be inspected and cleaned from operation floor.
Nozzles and spray pipe (efficiency and maintenance)
Dual FlowÂ
The cleaning efficiency is very high. The debris falls down in the hopper by the use of gravity. The water nozzles will clean the remaining debris by sending a fan of pressurised water down on the screen. The spray pipe is situated at the outside of the drum above the debris hopper. Nozzles do unfortunately block. With this flow pattern the nozzles are easily accessible by the operator for inspection, adjustment, cleaning or replacement without stopping the screen from revolving.
Centre FlowÂ
The debris falls down in the hopper by the use of gravity. The water nozzles will clean the remaining debris by sending a fan of pressurised water upwards, against gravity, on the screen. The spray pipe is situated at the inside of the drum at the height of the debris hopper. In this situation the water needs to go against gravity towards the debris hopper. This uses 30% more water pressure and capacity. The drum screen has to be stopped from revolving in order to reach the spray pipe and nozzles. Mechanics have to climb into the pit / drum screen to reach the nozzles, which can be complicated.
Check and replacement of main bearings (maintenance)
Dual Flow
With the dual flow the drum screen can be supported on the concrete foundation. The main bearings can be replaced and repaired without disabling the (complete) drum screen.
Centre FlowÂ
With a centre flow there are two types of shaft configurations that can be applied. When a rotating main shaft is applied, replacement is similar to the dual flow. In case of a fixed main shaft, which is applied by screens having a large diameter, this is more complicated because the bearings are located in the pit on the fixed hollow shaft and are charged with the full load. Therefore it’s difficult and time-consuming to replace these bearings.
Power consumption
Dual Flow
The revolving direction of the drum will be equal as the water flow, this will result in a low power consumption.
Centre Flow
At the centre flow the revolving direction of the drum is normally against the water flow, this results in a substantial increase of power consumption. This will potentially be two or three times higher, then when revolving direction is similar as the water flow.
Civil construction and clogging
Dual Flow
When debris blocks the screen panels and clogging appears, raw water level inside the drum will rise relative to the filtrated water. This water level difference will give a downward pressure on the civil work which supports the bearing base plates anchors (concrete is at its strongest in compression).
Centre Flow
With this flow pattern the rise of raw water is at the outside of the drum. Clogging will give an upward pressure. This ensures that the drum will float. There are tie down rods designed to break when the pressure on the drum is to high. If that happens the drum screen detaches and needs to be installed again. This could lead to production downtime and structural damage on the construction and/or screen.
On our download page you can find the comparison as PDF.