Water Intake Systems /
Screening Solutions
Water Intake Systems
Water intake systems are designed to mechanically clean or filter water extracted from seas, rivers, or lakes. This process involves removing entrained (floating) matter using screens or sieves, which prevents buildup, clogging, and abrasion in downstream stages. The primary goal is to safeguard suction pumps and other downstream equipment, such as desalination membranes, heat exchangers, condenser tubes, and related systems, from the carry-over of coarse and fine debris.
Water intake screening systems are used for filtering:
- cooling water for power plants (combined cycle, nuclear, thermal & hydro)
- process water for industrial production processes, like petrochemical plants and refineries.
Our intake screening machines are also used to filter raw water for various applications, including potable or drinking water plants, desalination plants, drainage channels, firefighting channels, and irrigation offtakes. Additional examples of their use include the food processing and mining industries.
A water intake system may consist of components such as sluice gates and stoplogs, coarse screens, micro drum screens, and traveling band screens. Below, you will find further details about these elements and their functionalities.
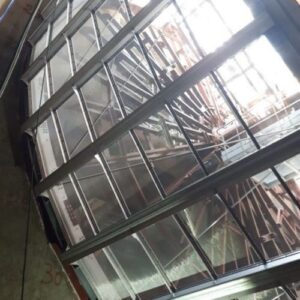
Typical layout of a water intake ‘screening train’
Hubert Water Intake System:
A ‘Screening Train’
We design, manufacture, and supply complete water intake ‘screening trains,’ including associated equipment and controls. A typical ‘train’ consists of:
Step 1: stoplog or sluice gate – closing chanel inlet for maintenance (downstream)
Step 2: coarse screens, static, cable hold and revolving screens – primary-filtration
Step 3: drum screen and / or travelling band screen – secondary / fine filtration
Step 4: stop log or sluice gate – closing chanel exit for maintenance (upstream)
Below, you will find an explanation of commonly applied subsystems.
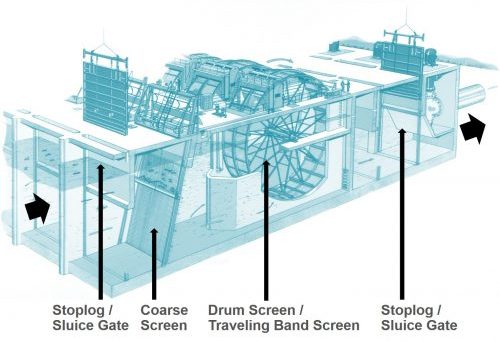
Stoplog and Sluice Gate
Hubert Stoplogs: Rapid and Secure Closure of Channels and Pump Chambers in Water Intake Systems
A Hubert stoplog (also referred to as a ‘stop gate’ or ‘penstock’) and sluice gate facilitate periodic inspection and maintenance of screening systems and pumps by allowing dewatering of the isolated section of the channel. Our stoplogs are custom-designed to meet client-specific requirements.
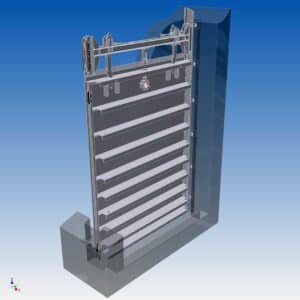
Coarse Screen
A Hubert Coarse screen: A Primary Filtration Screening System as Part of Water Intake Systems
This type of screen or rack serves as the initial barrier in a screening system, designed to endure and remove contamination ranging from large debris to relatively small particles. Such debris can be natural, like seaweed and jellyfish, or man-made, such as plastic waste.
Typically, it is a durable static bar rack that may include an automated trash rake system, either dedicated to individual screens or shared across multiple adjacent screens. Hubert offers a variety of coarse screens, customised to suit every (local) situation. Examples include static bar screens, revolving coarse screens, rotating rake screens, and cable-operated bar screens.
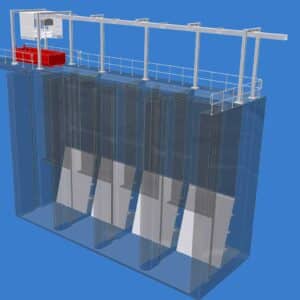
Drum Screen
Hubert Drum Screen: Efficient Filtration for Large Flow Rates
A drum screen is a self-cleaning, fully automated screen designed to filter very large flow rates with a relatively fine (secondary) filtration degree. Typical flow rates range from 40,000 to 120,000 m³/h per screen, depending on customer requirements and the specific local conditions at the intake. The filtration medium consists of woven mesh with a diameter of approximately 2–3 mm.
Hubert offers both vertical and horizontal drum screen applications, tailored to meet varying operational needs. The video provides a glimpse of a vertical drum screen during assembly.

Travelling Band Screen
Hubert Travelling Band Screen: a Compact Solution for Fine Filtration
A travelling band screen, also known as a “travelling water screen,” is specifically designed for fine (secondary) filtration of surface water. Due to its compact vertical construction, this type of screen requires minimal installation space, making it an ideal solution in locations where the total cleaning installation footprint is restricted. It is also well-suited for areas with significant variations between high and low water levels.
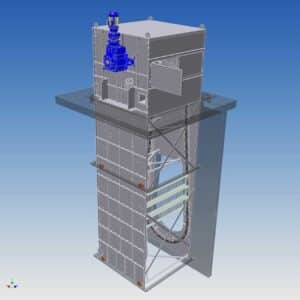